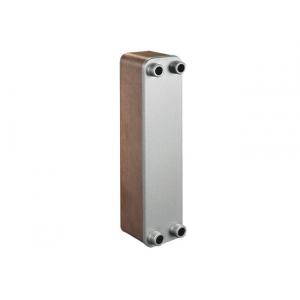
Add to Cart
Product description
Material of Plate | Suited Liquid Kinds | ||
Stainless Steel (AISI304.316 Etc) | Pure Water, Normal Water, Oil for eating, Mineral Oil | ||
Ti, Ti-pd | Sea Water, Saline Water, Mineral Water | ||
20Cr, 18Ni, 6Mo (254SMO) | Dilute Sulphuric Acid, Organic Water Solution | ||
Ni | High-temp and concentration caustic soda | ||
Hastelloy (C276, D205, B2G) | Concentration Sulphuric Acid, Hydrochloric acid, Phosphoric acid | ||
Material of Gasket | Operating Temperature ° C | Suited Liquid Kinds | |
NBR | -15~+135° C | Water, Sea Water, Mineral Oil, Salinous Water | |
EPDM | -25~+180° C | Hot Water, Steam, Acid, Alkali | |
F26 | -55~+230° C | Acid, Alkali | |
TPF | 0~+160° C | High Concentrated Acid, Alkali, High temperature Oil, Steam |
Applications
General heating and cooling duties. Hydraulic Oil Cooler.
Standard design
The plate heat exchanger consists of a pack of corrugated metal plates with portholes for the passage of the
two fluids between which heat transfer will take place. The plate pack is assembled between a fix frame plate
and a movable pressure plate and compressed by tightening bolts. The plates are fitted with a gasket which
seals the interpolate channel and directs the fluids into alternate channels. The number of plates is determined
by the flow rate, physical properties of the fluids, pressure drop and temperature program.
The plate corrugations promote fluid turbulence and support the plates against differential pressure. The frame
plate and the pressure plate are suspended from an upper carrying bar and located by a lower guiding bar, both
of which are fixed to a support column.
Connections are located in the frame plate or, if either or both fluids make more than a single pass within the unit,
in the frame and pressure plates.
Typical capacities
Liquid flow rate
Up to 16 kg/s (250 gpm), depending on media, permitted
Pressure drop and temperature program.
Water heating by steam
300 to 800 kW
Working principle
Channels are formed between the plates and the corner ports are arranged so that the two media flow through alternate
channels. The heat is transferred through the plate between the channels, and complete counter-current flow is created
for highest possible efficiency. The corrugation of the plates provides the passage between the plates, supports each
plate against the adjacent one and enhances the turbulence, resulting in efficient heat transfer.
Short delivery time.
High quality
Reasonable price
Customer made
Know-how design and customer support